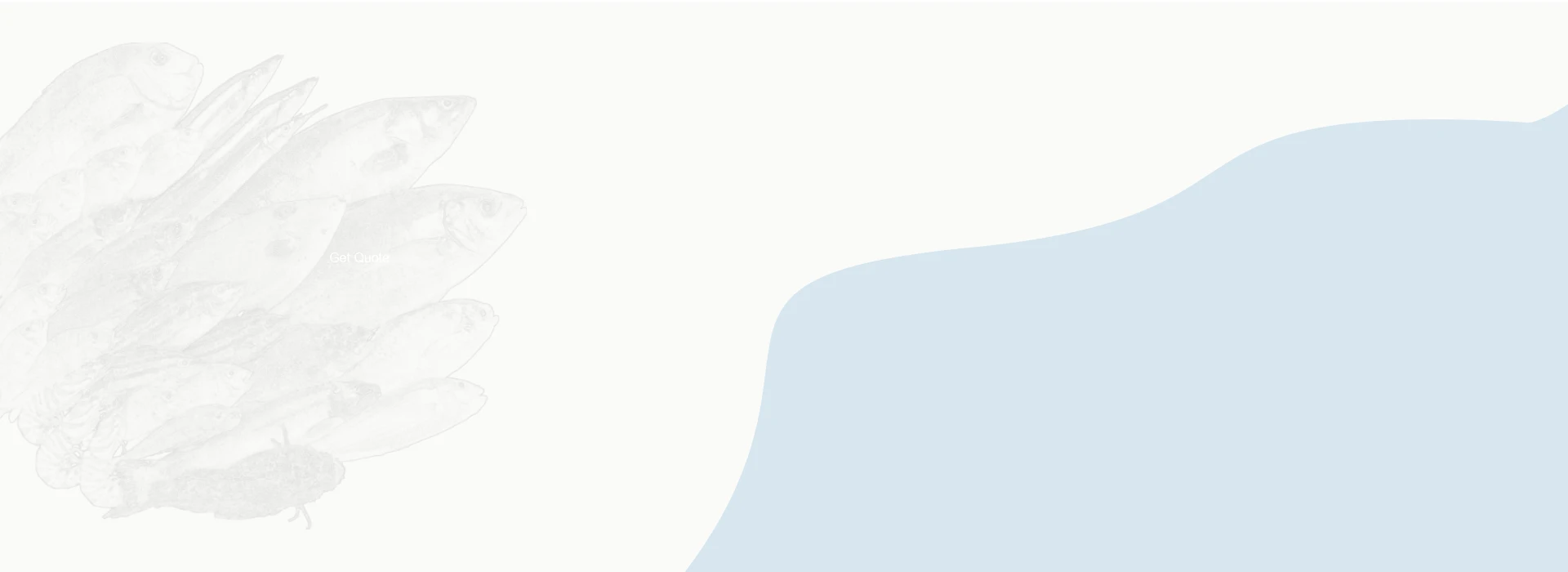
Wet Type Fish Feed Extruder
Wet type fish feed extruder is suitable for producing floating or sinking aquatic feeds such as fish, shrimp, eel, bullfrog, etc. It can also be used to process pet feeds such as dog food and cat food. It can process a variety of raw materials such as corn, soybean meal, fish meal, etc. The pellet diameter range is 0.9-15mm. The finished product is smooth and neat, has a long floating time, and does not pollute the water quality. It is widely used in medium and large feed factories and farms.
RICHI Machinery has over 30 years of expertise in feed machinery manufacturing, offering advanced wet extruders with stable performance, high output, and complete technical support for aquaculture feed plants worldwide.
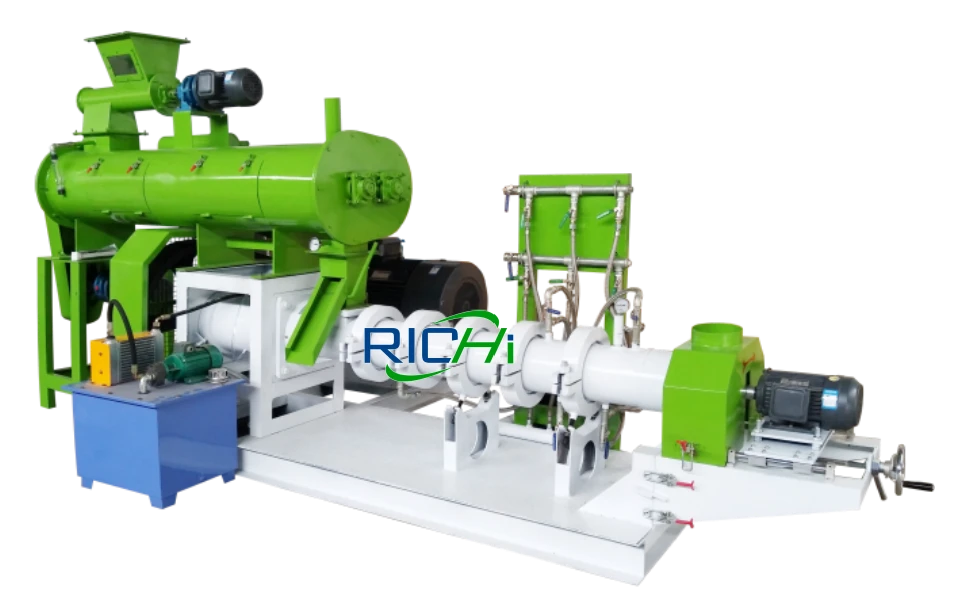
RICHI MACHINERY
What is a Wet Type Fish Feed Extruder?
A wet type fish feed extruder is a device dedicated to producing high-maturity floating or sinking fish feed pellets. It uses a process that combines steam and mechanical extrusion to fully condition and expand the raw materials, making the finished feed pellets more stable and easier to absorb nutrients. It is widely used in aquaculture farms, feed processing plants, and pet food production lines.
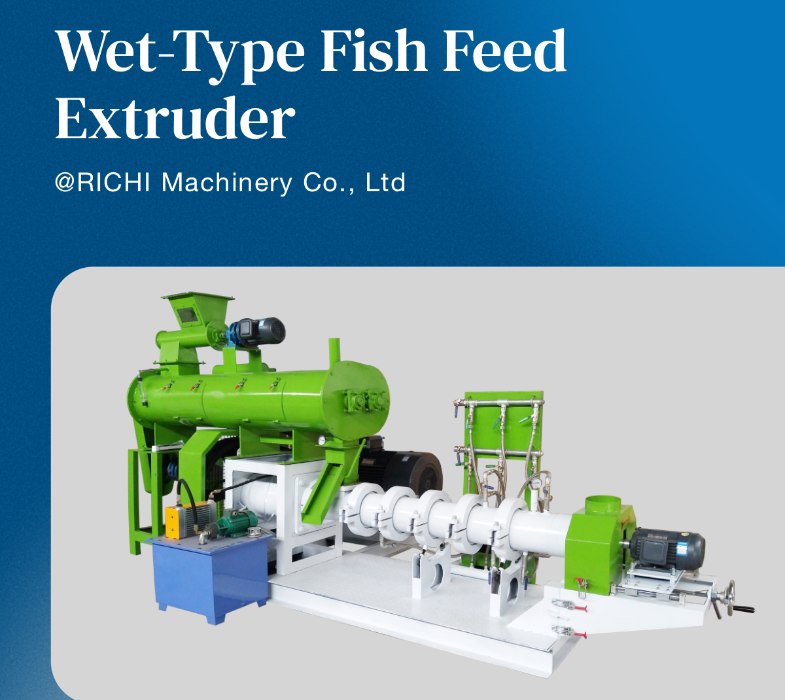
The wet type fish feed extruder pre-maturates the raw materials with high-temperature steam provided by the boiler, and then gelatinizes and expands the materials under the high-pressure shearing and high-speed rotation of the main screw, and finally extrudes them from the mold and cuts them into pellets by a cutter. The whole process not only improves the digestibility and stability of the feed in water, but also adjusts the floating and sinking state of the pellets according to the formula and process requirements.
At RICHI Machinery, floating fish feed extruders are divided into two types: single screw and twin screw. Among them, the single screw machine is further divided into two structures: dry and wet, which can flexibly match different production capacities and process requirements. Our equipment supports production from 500kg/h to more than 12t/h, and can produce floating, neutrally buoyant or sinking pellets to meet the feeding characteristics of different aquatic species, effectively reduce feed waste and improve breeding efficiency.
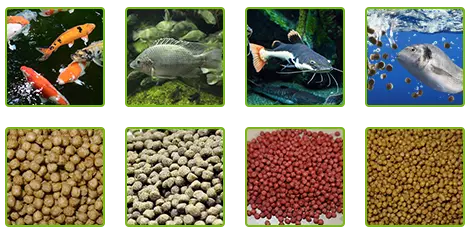
RICHI MACHINERY
Wet Type Fish Feed Extruder Applications
RICHI wet type fish feed extruder is comprehensive and widely applicable. It can meet the needs of many fish feed manufacturing plants and is also suitable for flexible use by farmers and investors. Whether it is fish feed, pet food, or livestock and poultry feed, it can easily cope with it and help you achieve the goal of efficient, safe and energy-saving feed processing.
Processable products
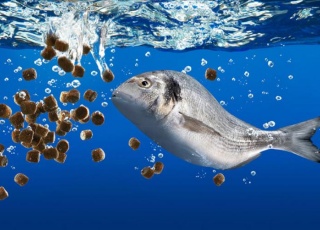
Floating fish feed
Pellets that can float on the water surface are suitable for various fish, improve feed utilization, reduce waste, and are easy to observe feeding conditions.
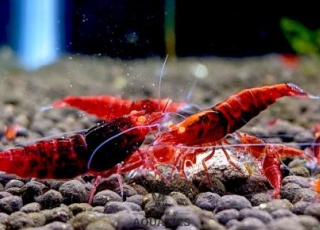
Small pellet feed for shrimp
Small pellets designed for shrimps have a controllable settling speed, meet the feeding habits of shrimps, maintain water quality, and improve survival rate.
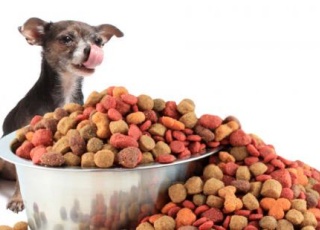
Pet pellet food
It can process dog food, cat food, and fish food of various shapes and tastes, which are comprehensive in nutrition and highly palatable, suitable for a variety of pets.
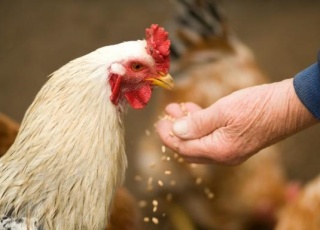
Poultry and livestock feed
Used to produce pellet feed for pigs, chickens, ducks and other animals, improve maturity and digestibility, and help animals grow healthily.
Suitable user groups
Feed mills
Medium and large feed processing enterprises require high output and high efficiency, suitable for batch standardized production.
Aquaculture farmers
Users with their own fish ponds, shrimp ponds, etc., suitable for self-use pelleting, control feed quality, and save feed procurement costs.
Small processing plants
Local feed workshops or regional suppliers, suitable for flexible processing to meet customized pellet feed needs.
Venture investors
Individual or corporate investment projects, simple equipment operation, short payback period, suitable for breeding or feed industry start-up.
RICHI MACHINERY
Technical Features of Wet Type Fish Feed Extruder
Wet type fish feed extruder is a key equipment in modern fish feed production lines, combining a variety of advanced technologies such as mechanical shearing, high temperature cooking and variable frequency control. In order to achieve uniform expansion, stable molding and high nutrition retention of pellet feed, RICHI Machinery has optimized the design of the core structural parts, making RICHI wet type fish feed extruder machine excellent in terms of output, pellet quality, energy efficiency, equipment life and ease of operation, and widely used in large-scale processing of feed products such as fish, shrimp and pets.
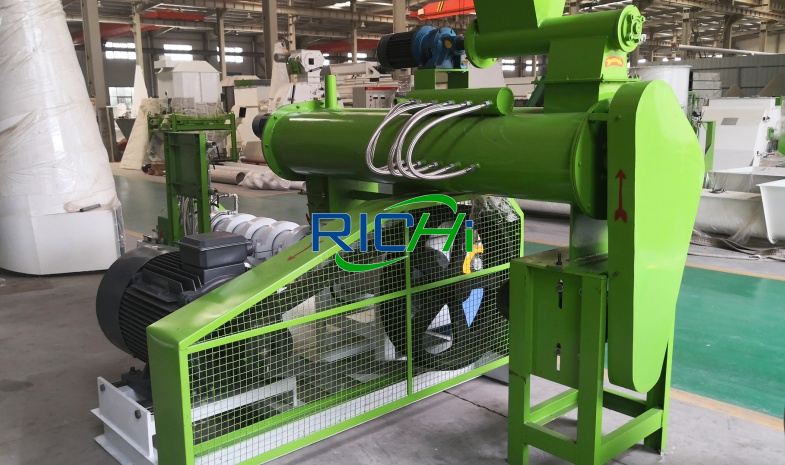
Variable Frequency Feeder
The equipment is equipped with a high-performance variable frequency motor and speed control system, which can adjust the feeding speed in real time according to material characteristics, output requirements and extrusion pressure. This precisely controlled feeding method can avoid problems such as material accumulation, blockage or uneven feeding, ensure the continuous, stable and efficient operation of the entire extrusion process, and improve the consistency of pellets and the stability of output. It is especially suitable for the production of feeds with complex formulas and large differences in powder density.
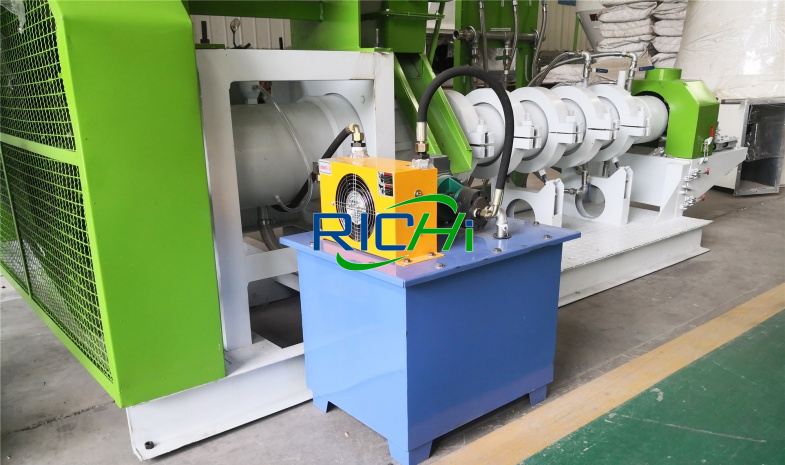
Double-layer jacketed stainless steel modulator
The modulator is located between the feeding device and the screw extrusion chamber. It adopts a double-layer stainless steel jacket structure, which can flexibly add steam, water or liquid nutrients to preheat, humidify and mature the raw materials. Through stirring, mixing and temperature control, the temperature and humidity of the material components are more uniform, creating ideal wet and hot conditions for extrusion, thereby significantly improving the puffing effect, pellet stability and palatability. This system is particularly suitable for the production of floating and slow-sinking fish feed and pet food with high requirements for appearance and nutrition.
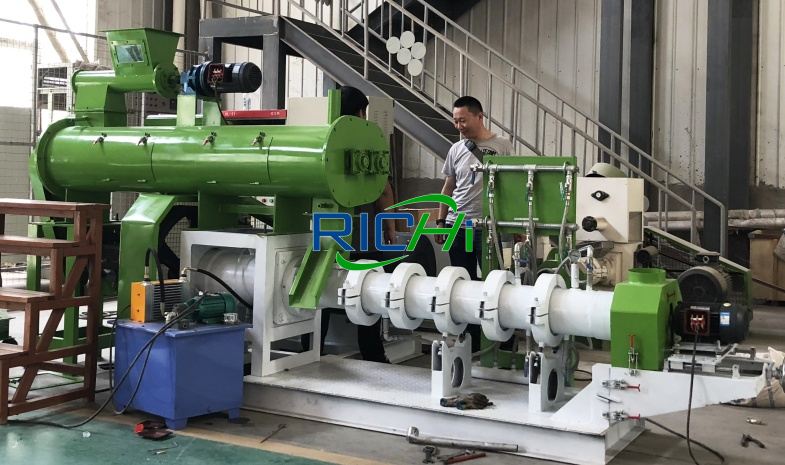
Durable Pelletizing Chamber
The interior of the pelletizing chamber is made of high-temperature resistant and wear-resistant alloy steel, which has extremely strong durability and structural stability. The screw adopts a segmented design, which can be flexibly combined according to different formulas to achieve a variety of puffing effects. The cutting system adopts a soft knife stepless speed regulation structure, which can easily adjust the pellet length, and the pellets are fuller and the edges are neater. The quick mold change design allows users to replace the discharge templates of different diameters to meet the production needs of pellets from 1mm to 30mm.
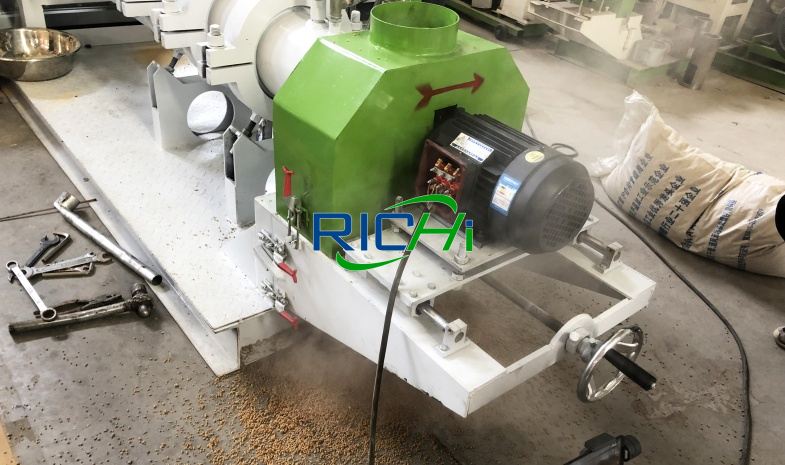
SIEMENS Main Motor
The main drive system uses Siemens motors, a world-renowned brand, with excellent power output and energy-saving effects. Its stable starting performance and long-lasting operating reliability can effectively ensure that the spindle can continue to work under high load and avoid downtime due to failure. Linked with the precision control system, it can monitor the speed and torque throughout the process, ensuring more precise control of mechanical energy and thermal energy during the extrusion process, thereby improving the overall working efficiency of the equipment and product consistency.
Technical Specifications of Wet Type Fish Feed Extruder
To meet the needs of aquatic feed production lines of different sizes, RICHI Machinery offers a variety of wet single screw extruders. This series of equipment has good energy efficiency and compact structure while maintaining high extrusion quality and stability, and is suitable for small to medium-sized feed processing projects. The following two devices both support the configuration of conditioners, variable frequency feeders and cutter systems, and adopt wear-resistant screw design to ensure production continuity and stability.
Model | DSP-90B | DSP-135B |
Main motor power (kw) | 37 | 75 |
Feeding power (kw) | 7.5 | 7.5 |
Tempering power (kw) | 1.1 | 2.2 |
Cutting power (kw) | 1.1 | 1.5 |
Screw diameter (mm) | 90 | 135 |
Machine size (mm) | 2600*1600*1900 | 3750*1980*1950 |
Output (T/H) | 0.5-0.6 | 0.8-1.0 |
Application | Suitable for small fish feed factories or aquaculture users with an output of 0.5-0.6 tons/hour, low energy consumption, compact footprint, suitable for the start-up stage or multi-variety low-volume production needs. | Designed for medium-volume needs, suitable for daily batch production, strong adaptability, and meets the mainstream scale needs of commercial aquatic feed processing. |
RICHI MACHINERY
Related Project Cases of Wet Type Fish Feed Extruder
With the growing demand for high-quality and efficient feed processing equipment in the global aquaculture industry, RICHI wet fish feed extruders and supporting floating fish feed production lines have been successfully put into operation in many countries. The following are some typical project cases, covering different production capacities and different application scenarios, which fully demonstrate the advancement and adaptability of the equipment.
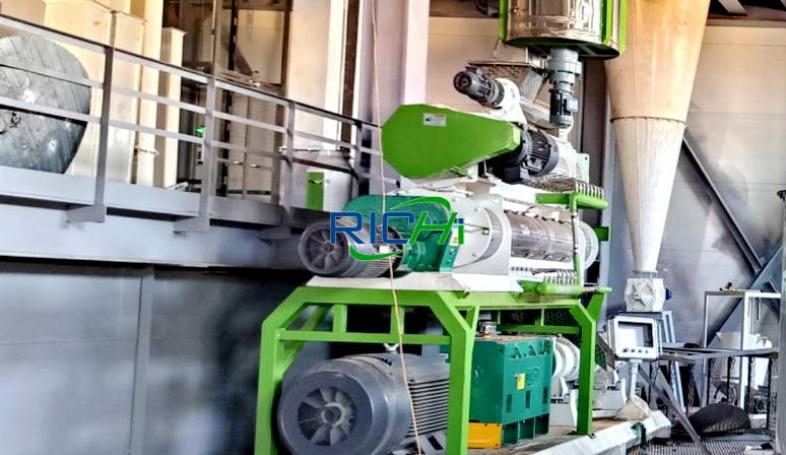
1.5~2 tons/hour floating fish feed intelligent processing line
- Country: United States
- Type: RICHI wet fish feed extruder + floating fish feed production line
- Main equipment: wet extruder, variable frequency feeder, double jacket conditioner, dryer, cooler, oil sprayer, automatic packaging system
- Raw materials: corn meal, fish meal, soybean meal, wheat bran, vegetable oil
- Pellet diameter: 1.5 mm, 6.0 mm
- Production time: 60 days
- Operator configuration: 4 people
- Customer feedback: The whole production line has a high degree of intelligence, good pellet forming rate, strong floating property, stable supply to multiple freshwater aquaculture bases, and the product has obtained USDA compliance qualifications
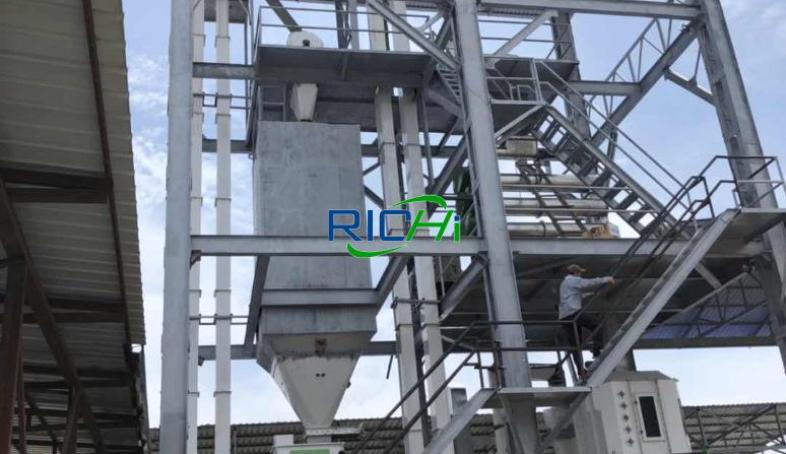
2 tons/hour environmentally friendly floating fish feed production line
- Country: Germany
- Type: RICHI wet fish feed extruder + European standard floating fish feed production line
- Main equipment: Wet extruder, double-layer conditioning system, precision cutter, energy-saving drying and cooling combination, automatic weighing and packaging system
- Raw materials: corn, soybean meal, fish meal, flaxseed meal, vitamin premix
- Pellet diameter: 2.0 mm, 8.0 mm
- Production time: 90 days
- Operator configuration: 5 people
- Customer feedback: Feed pellets have high extrusion degree and good stability, and the floating time in water exceeds 12 hours, meeting EU environmental protection breeding standards, and the export ratio exceeds 30%
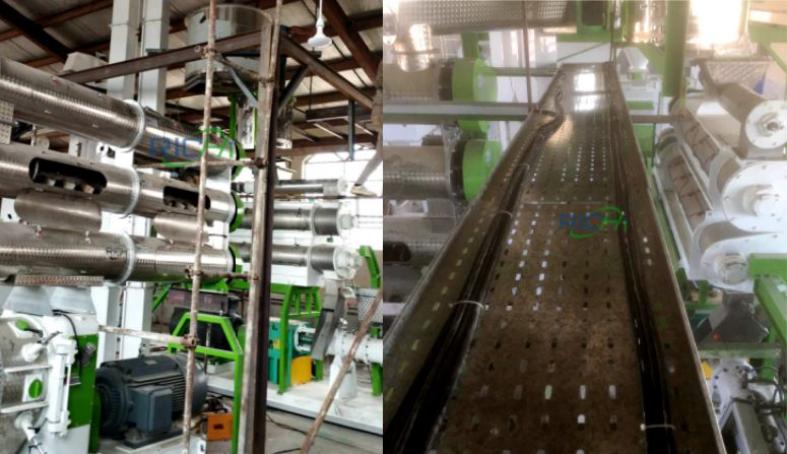
0.5 ton/hour small floating fish feed precision production line
- Country: Japan
- Type: RICHI wet fish feed extruder + small floating fish feed production line
- Main equipment: wet extruder main machine, variable frequency feeding, fine conditioning, drying and cooling integrated system, small packaging machine
- Raw materials: corn meal, fish meal, soy protein, wheat bran, natural attractant
- Pellet diameter: 1.2 mm, 4.0 mm
- Production time: 45 days
- Operator configuration: 3 people
- Customer feedback: The equipment runs quietly and efficiently, especially suitable for ornamental fish feed. The finished product is uniform and has strong palatability, successfully replacing imported brands locally
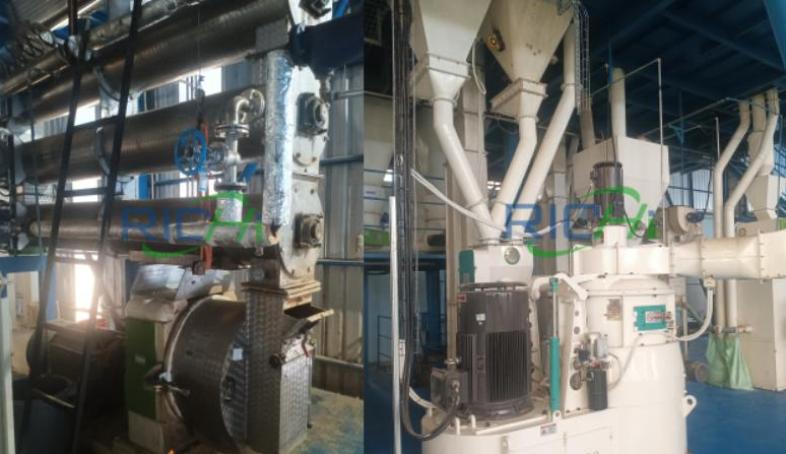
2 tons/hour commercial floating fish feed fully automatic production line
- Country: Canada
- Type: RICHI wet fish feed extruder + automatic floating fish feed production line
- Main equipment: wet extruder, double conditioner, automatic oil spray system, variable frequency cutting device, combined drying and cooling system, automatic packaging line
- Raw materials: fish meal, corn protein meal, soybean meal, rapeseed meal, fish oil, trace additives
- Pellet diameter: 2.0 mm, 10.0 mm
- Production time: 70 days
- Operator configuration: 4 people
- Customer feedback: The factory production line is highly automated, the product quality is stable, and it is suitable for trout and salmon farming needs. It has now formed a branded batch export model
Wet Type Fish Feed Extruder Production Process Design
The wet type fish feed production line realizes the continuous and automated production of high-quality aquatic feed through multiple links such as raw material processing, extrusion, drying and cooling, coating and packaging. As the core equipment of the aqua feed plant, the wet type fish feed extruder effectively improves the maturity and stability of pellets in water through high-temperature steam conditioning and high-pressure puffing, which is the key guarantee for the production capacity and product quality of the entire line. The scientific and reasonable process not only improves the quality of feed and production efficiency, but also effectively reduces energy consumption and costs, and enhances the competitiveness of enterprises.
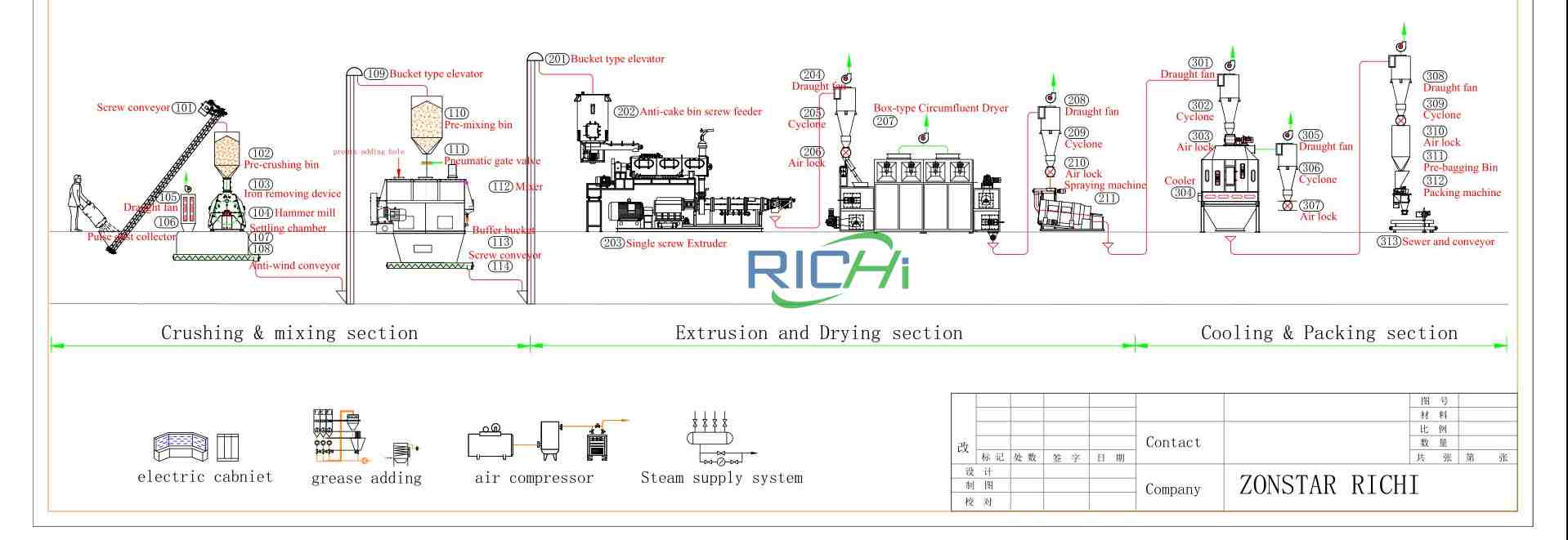
01 Raw material receiving and cleaning
Production starts with raw material receiving, including weighing, testing, unloading and other links. To ensure the quality of raw materials and equipment safety, magnetic separators, screeners, dust collectors and other equipment are required to clean the raw materials to remove impurities such as stones, metals, dust, etc., to ensure the smooth progress of subsequent processing.
02 Storage and crushing
The cleaned corn, wheat, soybean meal and other raw materials are stored in silos or silos to ensure production continuity. The raw materials are then refined by crushing equipment to increase their specific surface area, enhance nutrient absorption rate and subsequent process efficiency. Fine grinding or ultrafine grinding can also be performed according to formula requirements.
03 Batching and mixing
Automatic or semi-automatic batch processing systems are used to accurately weigh various raw materials and batch them once or twice. Then, high-efficiency mixers are used to fully mix the dry and liquid ingredients to ensure that the feed formula is uniform and consistent to meet the comprehensive nutritional needs of aquatic animals.
04 Steam conditioning and extrusion molding
Wet fish feed extruders are used for core processing. The raw materials are pre-treated with high temperature and high humidity by steam conditioner to denature protein and gelatinize starch. Then the raw materials are heated and pressed in the screw system, expanded and formed into fish feed pellets of different density and shape (floating, sinking or slow sinking).
05 Drying and cooling
The moisture content of the expanded pellets is high, and the moisture needs to be reduced to a safe range by multi-layer dryer to extend the shelf life. Then the pellets are cooled to near room temperature by countercurrent cooling system to enhance their mechanical strength and prevent agglomeration and mildew.
06 Liquid spraying and screening
After the pellets are cooled, oil, vitamins and other ingredients are added by spraying equipment to improve the palatability and nutritional value of the feed. Then fine powder and large pellets are screened out, and the unqualified part is refluxed to ensure the consistency of product pellet size and realize efficient recycling of resources.
07 Automatic measurement and packaging
Qualified pellets are weighed, sealed and coded by automatic packaging system, and can be discharged in bag, ton bag or bulk. It is suitable for sales-oriented feed production, and can also be configured with simple packaging or bulk systems according to needs to meet the needs of farms.
If you are planning to build an aquatic feed factory or upgrade an existing production line, RICHI Machinery can provide you with a full set of solutions from process design, equipment selection to whole-line installation and commissioning. Welcome to contact us for customized technical services.
RICHI MACHINERY
Difference Between Dry Type and Wet Type Fish Feed Extruder
In fish feed processing, fish feed extruder is one of the key equipment in floating fish feed plant. According to whether steam conditioning is used in the processing process, extruders can be divided into two types: wet type fish feed extruder and dry type fish feed extruder. They have their own advantages in working principle, scope of application, pellet quality, etc., and are suitable for different production needs.

Different heating methods
The wet type feed extruder pellet machine uses an external steam boiler to inject steam or water into the raw material in the conditioner so that the material is fully matured before entering the extruder main machine. In contrast, the dry type extruder does not rely on external heat source, and mainly relies on mechanical friction when the screw rotates to generate heat to heat the material. Since there is no steam system, the dry type machine has a simpler structure and is easy to start.

Differences in raw material moisture and maturation effect
The moisture content of raw materials processed by wet machines generally reaches more than 20% to 30%, and high-temperature cooking makes the pellets highly mature and easier to absorb nutrients; dry machines control the moisture content of raw materials to about 15% to 20%. Although puffing can also be achieved, the degree of maturation is relatively low, which is more suitable for ordinary feed or short-term use needs.

Comparison of pellet quality and palatability
The pellets extruded by wet extrusion have a more stable structure, adjustable density, good palatability, and can meet the feeding needs of fish in different water layers (floating, neutral, and sinking pellets). At the same time, high-temperature treatment also helps to kill harmful bacteria such as Salmonella and improve feed safety. Dry pellets are mostly light and floating, with slightly inferior puffing effects, and are more suitable for low-cost, non-high-end feed products.

Applicable objects and investment costs
Wet type fish feed extruder machines are generally used in medium and large aquatic feed factories and commercial pet food production lines, suitable for customers with large production capacity and high quality requirements. It is fully equipped, but has certain requirements for infrastructure, such as boilers, water sources, steam systems, etc. The dry fish feed extruder is more suitable for small farms, start-ups or users with limited budgets. It has the advantages of small investment, small footprint and simple operation.
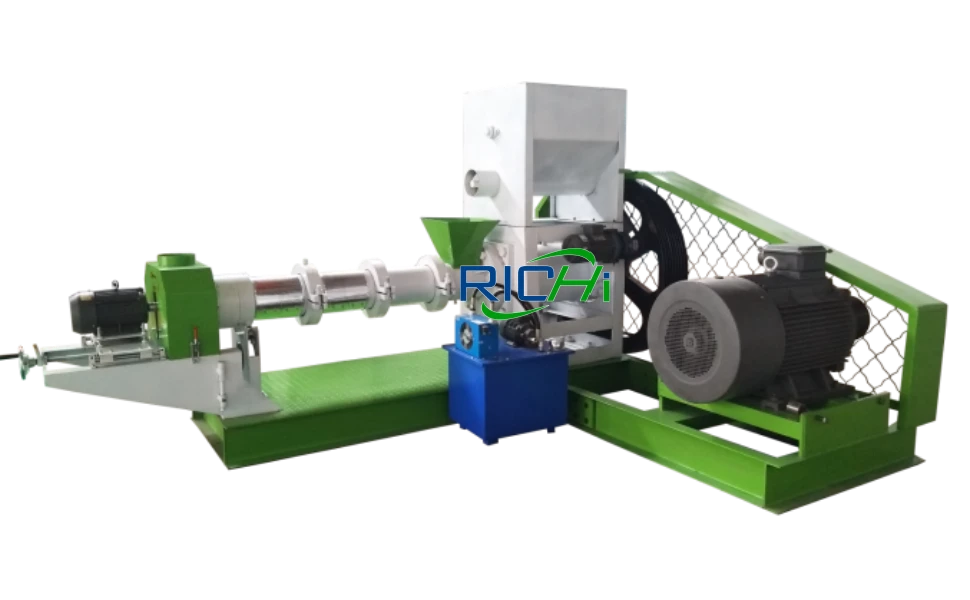
Dry Type Fish Feed Extruder
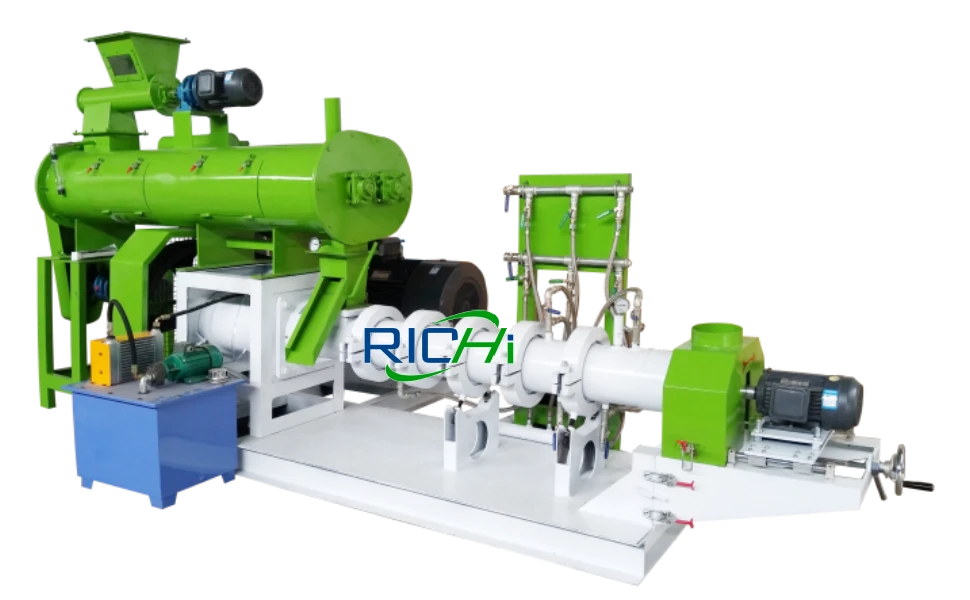
Wet Type Fish Feed Extruder
Related videos on Wet Type Fish Feed Extruder
To help you better understand how our wet fish feed extruders work in real production scenarios, we have selected a series of equipment demonstration and trial operation videos. These videos not only show the entire production process from raw material processing to final pellet output, but also highlight the efficiency and versatility of our extrusion systems. Whether producing floating fish feed, sinking feed or special shrimp feed pellets, you can clearly see how each device operates, how the pellets are formed, and how the finished product meets various aquaculture needs.
Floating Fish Feed Pellet Line in Iran——floating fish feed extruder machine
Automatic Prawn Feed Pellet Production Line——Prawn Feed Making Machine
Sinking Fish Feed Machine Trial Run——sinking fish feed machine
Fish Feed Production Line——fish feed pellet making machine
RICHI MACHINERY
Why Choose RICHI Machinery
Choosing RICHI Machinery means you’ll receive not only high – quality equipment but also one – stop solutions and comprehensive service support. Here are some key reasons to choose us:
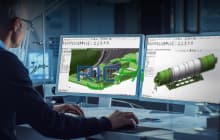
30 years of industry experience
Since its establishment in 1995, RICHI Machinery has amassed 30 years of rich experience in the design, production, and R & D of wet type fish feed extruder. With our profound technical accumulation and global development, we can provide our customers with reliable equipment and solutions.
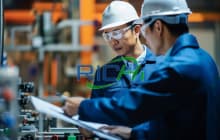
Customized turnkey solutions
We offer a complete turnkey production line, covering project design, equipment manufacturing, installation and commissioning, and personnel training, according to your specific needs. Whether it’s a small farm or a large feed factory, we can tailor a suitable production plan for you.
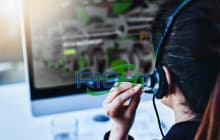
Complete after – sales service
We have a comprehensive after – sales system, providing you with all – round services from pre – sales consultation to after – sales maintenance. This includes professional and systematic training to help you quickly master equipment operation and maintenance skills and maximize project requirements.
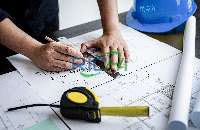
Built Around Your Needs
We can create customized turnkey pellet production line projects based on your unique requirements. For example, in this project, we provided customized technical solutions and operation training for the wet type fish feed mill to help the production line operate stably in the long term. You can find us on YouTube.