animal feed processing plant
The Key Force Driving the Upgrading of the Breeding Industry
The RICHI animal feed processing plant can produce feed pellets with sizes ranging from 2 to 12 mm, meeting the feeding requirements of different breeding animals. It features high production efficiency, with an hourly output of 1 – 40 tons. This production line is widely used in various feed manufacturing plants and feed processing lines. Thanks to its excellent performance, it has become the trusted choice of many feed production companies. It can effectively boost production efficiency, assist companies in expanding their production scale, and enhance their market competitiveness.

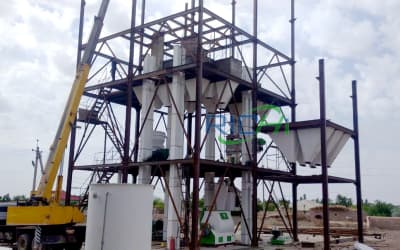
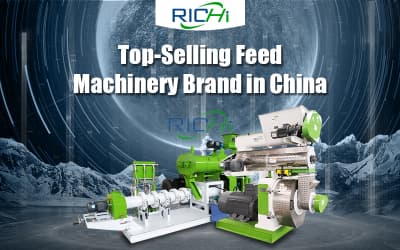
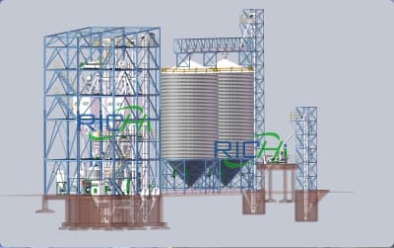
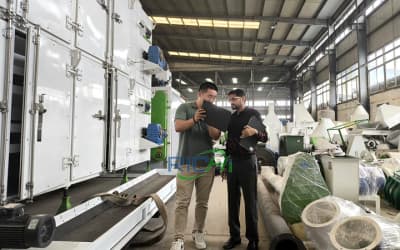
animal feed processing plant
— Richi Machinery —
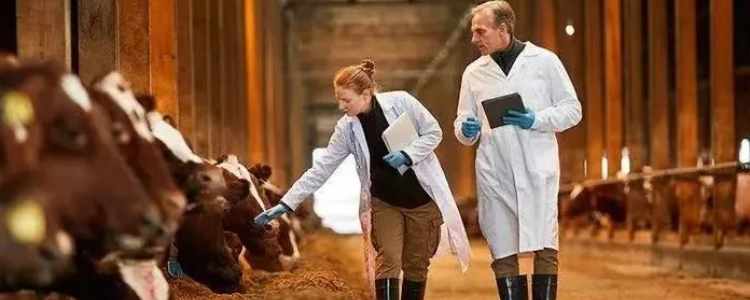
animal feed processing plant: The Core Engine of Modern Aquaculture
As the core equipment of the animal husbandry industry, the animal feed production line is propelling the development of the global breeding industry with its efficient, intelligent, and environmentally – friendly characteristics. Choosing a high – quality feed processing plant is not merely about selecting a device; it’s about opting for an efficient, intelligent, and environmentally – friendly breeding future.
Feed processing plants have emerged as the key to improving production efficiency, ensuring a balanced supply of animal nutrition, and reducing comprehensive production costs. As a professional feed machinery manufacturer with 27 years of in – depth experience in the industry, RICHI Machinery leverages its profound technical accumulation and rich practical experience to serve customers in over 150 countries worldwide.

What is an animal feed processing plant?
An animal feed plant is a combination of equipment and a process flow dedicated to processing various animal feeds. It encompasses processes such as raw material crushing, mixing, pressing, cooling, and packaging. It can accurately process and convert a variety of raw materials, like grains, proteins, and vitamins, into high – quality and uniform pelletized feed.
The feed it produces is widely applied in different breeding fields, including poultry (such as chickens), animal husbandry (such as cattle, pigs, and rabbits), and aquatic products (such as fish and shrimp). Thanks to its automation and high efficiency, this production line enhances the quality and output of feed production. The pellet feed produced is nutritious, easy to digest, absorb, store, and transport, providing a healthier and more nutritious feed option for the breeding industry.
111
RICHI MACHINERY
Application Areas of the animal feed processing plant
The feed pellet line is an efficient and multifunctional piece of equipment widely used in the feed processing industry. Its main application areas and features are as follows:
Raw Material Treatment
The feed pellet production line can process a wide range of raw materials, including but not limited to corn, wheat, oilseed powder, and corn stalks. These materials are selected for their nutritional value and local availability, helping to reduce production costs while maintaining feed quality.
These ingredients are first crushed and mixed, then processed into uniform and nutrient-rich feed pellets. The pellets are easy to digest, reduce waste, and help improve animal growth and feed efficiency.
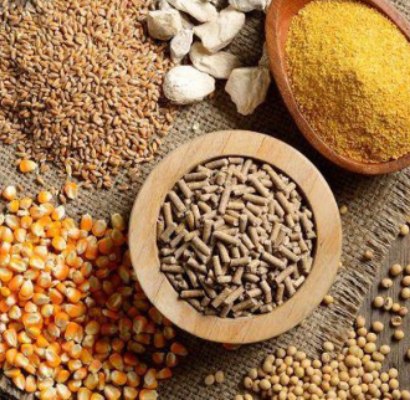
RICHI
Animal Feed Production
This production line is capable of producing feed pellets for almost all animal species. For example:
Chicken feed pellets: The pellet diameter is 2 – 4 mm.
Boat feed pellets: The pellet diameter generally falls between 4 – 8 mm.
Fish feed pellets: Suitable for aquaculture, and the pellet size can be adjusted according to the needs of different fish.
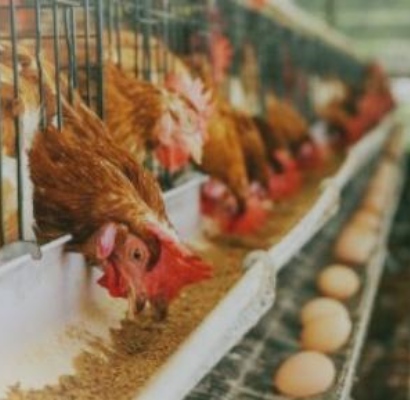
RICHI
Application Scenarios
Large feed factory: Meets the requirements of large – scale production.
Medium – sized feeding factory: Adapted to medium – scale breeding production.
Animal Farm: Provides customized feed solutions for the farm.
Personal feeder: Small feed pellet machines are also suitable for personal feeders, meeting the needs of small – scale breeding.
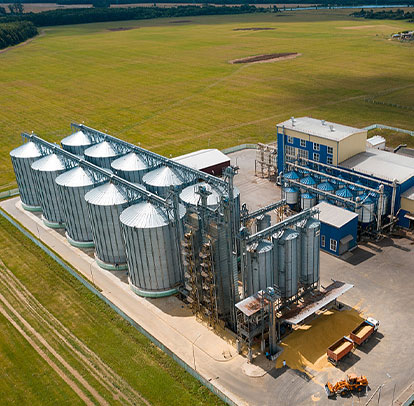
RICHI
RICHI MACHINERY
Why do we need an animal feed processing plant?
In the process of the modern livestock and poultry breeding industry’s transformation towards large – scale and scientific development, feed pellet production lines are the core support for achieving efficient breeding. This is mainly reflected in the following aspects:
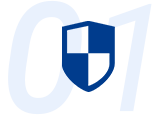
Let the animals eat well and grow fast
The granule production line can scientifically combine raw materials such as grains and proteins to make granule feed of a consistent size. In this way, animals can consume a balanced diet with every bite, grow faster and stronger, and there is less feed waste. Compared with traditional powdered feed, pelleted feed can increase the growth rate of livestock and poultry and improve feed utilization efficiency.
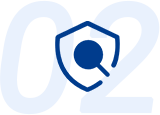
Less waste, safer, and protect the breeding environment
Pellet feed has a regular shape, making it less likely for animals to be picky eaters, and significantly reducing feed waste. Moreover, pellet feed is less prone to mildew and spoilage, and is more convenient for storage and transportation. The high – temperature production process can kill various harmful bacteria, reducing animal diseases and the use of antibiotics. This not only safeguards animal health but also reduces environmental pollution.
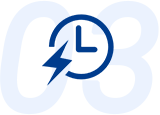
Keep up with new breeding trends and sustainable development
Currently, the global demand for meat is on the rise, while traditional feed production is slow and less safe, unable to meet the demand. The granular production line can stably produce high – quality feed, and can also turn waste such as straw and rice husks into valuable resources, reducing pollution and saving resources. It conforms to the general trend of green breeding, enabling the breeding industry to develop sustainably in the long term.
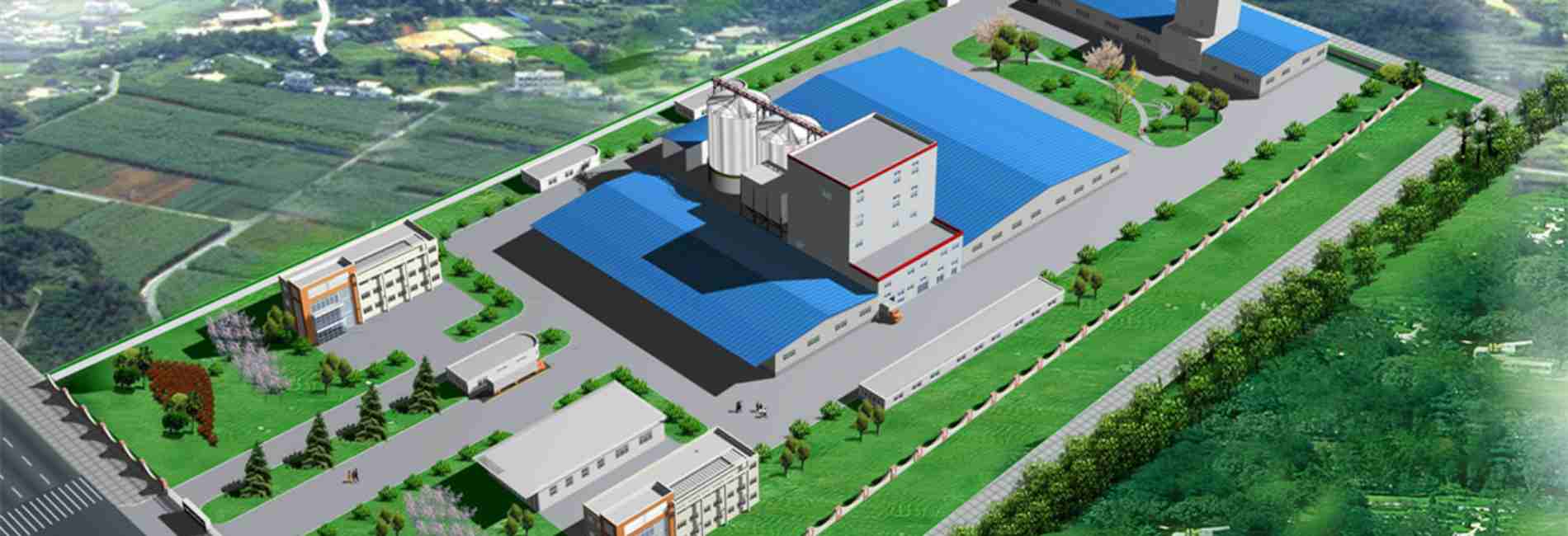
Characteristics of the animal feed processing plant
Simple operation and low labor consumption
In animal feed processing plant, Small production lines only require 1 – 2 people, and large production lines need 5 – 10 people. This can effectively cut labor costs and make production more efficient and convenient.
Reasonable process and easy installation
With a scientific process design, small production lines don’t need on – site civil engineering and welding. This simplifies the installation process, shortens the installation cycle, and allows for quick commissioning.
Excellent structure
It has a novel, compact structure with a reasonable layout. It’s easy to operate and maintain, has high safety, a low failure rate, is made of high – quality materials, and has a long service life.
Wide applications
It can produce feed pellets for various animals like chickens, cattle, fish, shrimp, and pigs, meeting the feed requirements in different breeding scenarios.
Saving space and cost
It has a small footprint, doesn’t take up too much space. The production speed can be adjusted as needed, and it can be customized according to customer requirements to maximize cost savings.
Environmentally friendly and well-configured
It comes with a dust removal system to protect the working environment and uses high – quality accessories such as SKF bearings and Siemens motors to ensure stable operation and high – performance output.
Diverse applications
Suitable for feed production plants, farms, and individuals with different – scale animal breeding, it can meet a wide range of feed production needs.
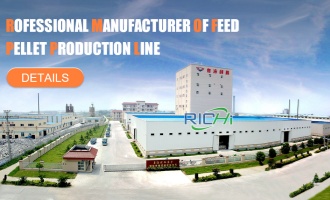
Characteristics
Simple operation and low labor consumption
Reasonable process and easy installation
Excellent structure
Wide applications
Saving space and cost
Environmentally friendly and well-configured
Diverse applications
RICHI MACHINERY
Global Demand and Future Development Trends of animal feed processing plants
With the growth of the global population and the improvement of living standards, the demand for animal – derived foods such as meat, eggs, and milk continues to increase. The market size of the feed industry is huge and growing steadily. As the core equipment for feed production, the demand for feed pellet production lines has also shown a significant growth trend.
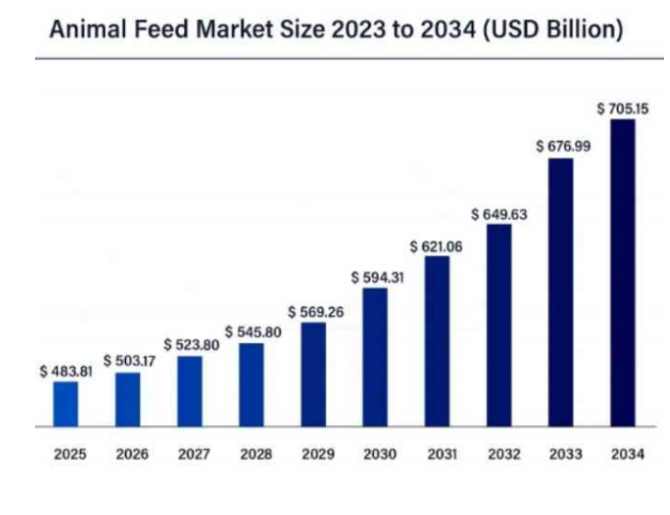
Global animal feed processing plant Demand
1. Population growth and increased demand for animal protein
The continuous growth of the global population has driven up the demand for animal protein, which in turn has spurred the development of the feed industry.
2. Modernization and large – scale development of animal husbandry
The modernization and large – scale development of animal husbandry have led to an increased demand for efficient and intelligent feed processing plants in breeding farms. Large farms need more efficient feed production systems to meet the requirements of large – scale farming.
3. Diversified feed products and high – quality demand
As consumers’ requirements for livestock products improve, the demand for high – quality feed is gradually increasing. This has prompted feed production companies to continuously upgrade their production lines to meet the market’s demand for personalized and customized feeds. For example, compound feed is popular among farmers due to its balanced nutrition and ease of use, and its output accounts for a large proportion of the total feed output.
4. Environmental protection and sustainable development requirements
With the enhancement of environmental awareness and the strengthening of environmental protection policies, the feed production industry pays more attention to green production and sustainable development. This has driven the demand for environmentally friendly feed pellet production lines that can reduce environmental pollution during the production process.
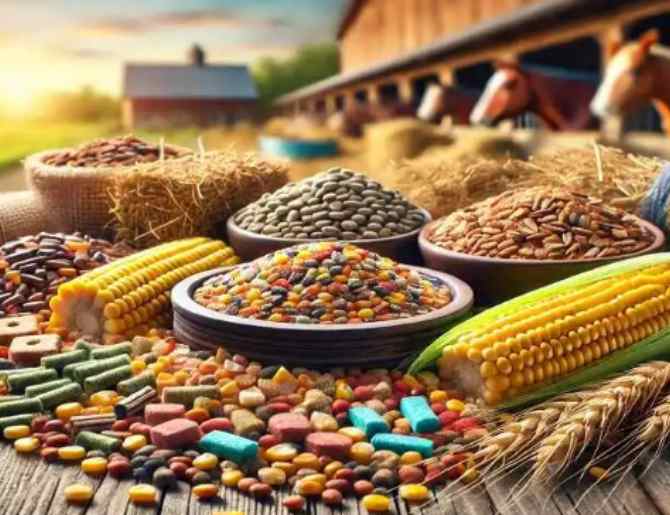
Future Development Trends
1. Technological innovation and industrial upgrading
The feed pellet line will become more high – end and intelligent. By introducing advanced biotechnology, information technology, and intelligent manufacturing technology, production efficiency and product quality will be improved.
2. Green production and sustainable development
The feed production industry will develop in a high – performance, environmentally friendly, and green direction. There will be a focus on developing low – phosphorus and low – nitrogen emission feed products to reduce environmental pollution.
3. Market demand growth and consumption upgrading
With the growth of the global population and consumption upgrading, the animal feed plant market will have broader development space. The demand for high – quality, personalized, and customized feed is increasing, which promotes feed production companies to continuously upgrade their production lines.
4. International development and market expansion
With the integration of the global economy, the international development trend of the feed production industry is becoming more and more obvious. Chinese feed companies will accelerate their internationalization pace, actively participate in international competition and cooperation, and expand overseas markets.
RICHI MACHINERY
Why Choose RICHI Machinery
Choosing RICHI Machinery means you’ll receive not only high – quality equipment but also one – stop solutions and comprehensive service support. Here are some key reasons to choose us:
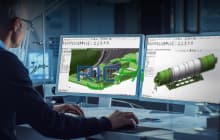
30 years of industry experience
Since its establishment in 1995, RICHI Machinery has amassed 30 years of rich experience in the design, production, and R & D of animal feed pellet machinery. With our profound technical accumulation and global development, we can provide our customers with reliable equipment and solutions.
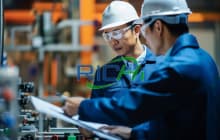
Customized turnkey solutions
We offer a complete turnkey production line, covering project design, equipment manufacturing, installation and commissioning, and personnel training, according to your specific needs. Whether it’s a small farm or a large feed factory, we can tailor a suitable production plan for you.
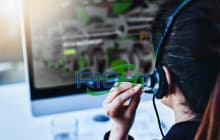
Complete after – sales service
We have a comprehensive after – sales system, providing you with all – round services from pre – sales consultation to after – sales maintenance. This includes professional and systematic training to help you quickly master equipment operation and maintenance skills and maximize project requirements.
Main Equipment of the animal feed processing plant
— Richi Machinery —
The animal feed processing plant consists of multiple key pieces of equipment, each with a specific function to ensure the smooth progress of the entire production process.
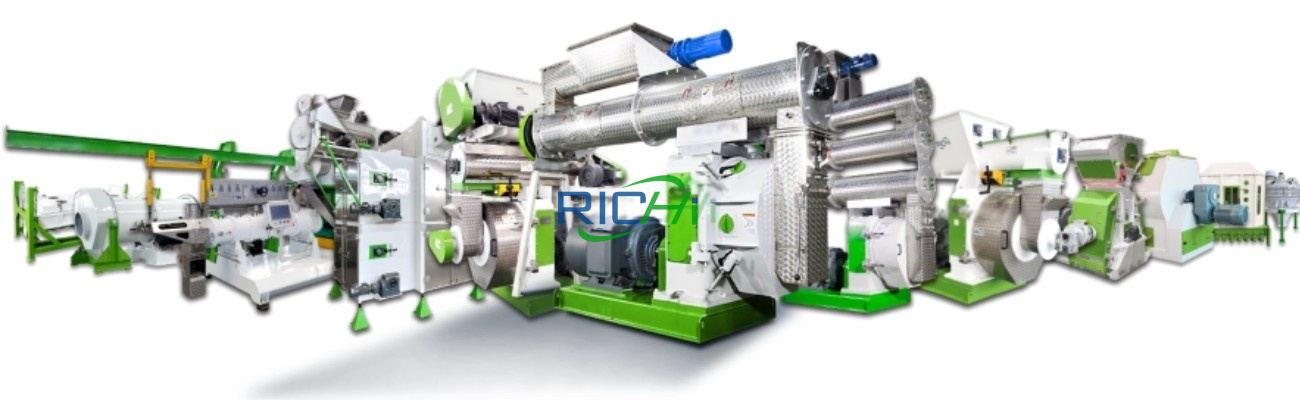
(1) Drum – type first – level cleaner
Used to remove large debris from raw materials, such as straw, hemp rope, and corn cobs, to protect subsequent equipment from damage.
(2) Permanent magnet cylinder
Cleans up magnetic metal inclusions like iron filings in raw materials to prevent damage to the granulation equipment.
(3) Bucket elevator
Lifts the raw materials vertically to the specified height for easy subsequent processing.
(4) Pulse dust collector
Reduces the dust generated during production, improves the working environment, and reduces dust pollution.
(5) Single – axle paddle mixer
Mixes the raw materials evenly and adopts a double – layer rotor design to ensure the mixing effect.
(6) Ingredient scale
Achieves accurate ingredients, reduces overall ingredient errors, and ensures balanced feed nutrition.
(7) Animal feed granulator
Designed and manufactured using new technologies and materials, it presses the tempered raw materials into pellets under the pressure of the ring mold and the pressing roller.
(8) Countercurrent cooler
Using the countercurrent cooling principle, it cools high – temperature and high – humidity feed pellets to room temperature to prevent the surface of the pellets from cracking.
(9) Automatic packaging system
Realizes the automatic packaging of feed pellets, improving packaging accuracy and speed.
RICHI MACHINERY
Core Equipment of the animal feed processing plant
In the production process of feed pellets, many key pieces of equipment are involved. They work in tandem to ensure the efficient operation of the feed pellet production line and the high – quality output of feed products. The following is a detailed introduction to these core and main equipment:
Richi Machinery
animal feed pellet making machine
The animal feed pellet making machine is undoubtedly the core equipment in the entire feed processing line. Its performance directly affects the quality of feed pellets. RICHI Machinery’s animal feed pellet machine is carefully designed and manufactured using new technologies and materials. Notably, the ring molds, rollers, and doors of its granulation chamber are made of stainless steel, which offers good durability, stability, and hygiene.
The working principle of this machine is to first temper the raw materials to a certain temperature and humidity. Then, the strong extrusion pressure between the ring die and the pressing roller forces the raw materials to pass through the die holes on the ring die, finally forming feed pellets with a regular shape and uniform size.
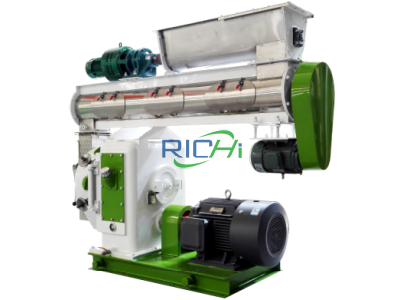
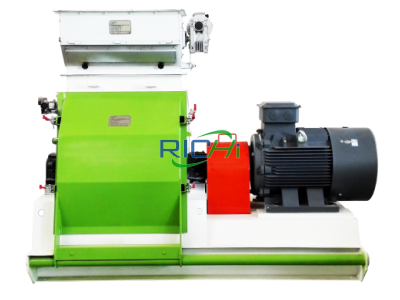
Hammer Crusher
As an excellent – performing hammer grinder, the RICHI water drop hammer grinder has strong crushing capabilities. It can crush almost all common feed raw materials, such as corn, wheat, beans, and crushed cakes, and process them into powder, providing ideal raw material conditions for the subsequent granulation process to ensure the best granulation effect. Moreover, the equipment also has many advantages like high efficiency, low labor consumption, and a small footprint, further enhancing the overall efficiency and cost – effectiveness of feed production.

We care about what you need
The core equipment and main equipment of the animal feed plant together form a complete feed production process. From raw material processing to final packaging, each device plays an essential role. Choosing high – quality equipment can not only improve production efficiency but also ensure the quality and stability of feed. If you are interested in feed pellet production lines or have custom requirements, please feel free to contact us, and we will provide you with professional solutions.
Working Process of 1-2T/H animal feed processing plant
Small – capacity feed pellet production lines are usually suitable for small farms or individual breeders, with a production capacity generally ranging from 1 – 2 tons per hour. The following are the main work processes of the small – capacity feed pellet production line:
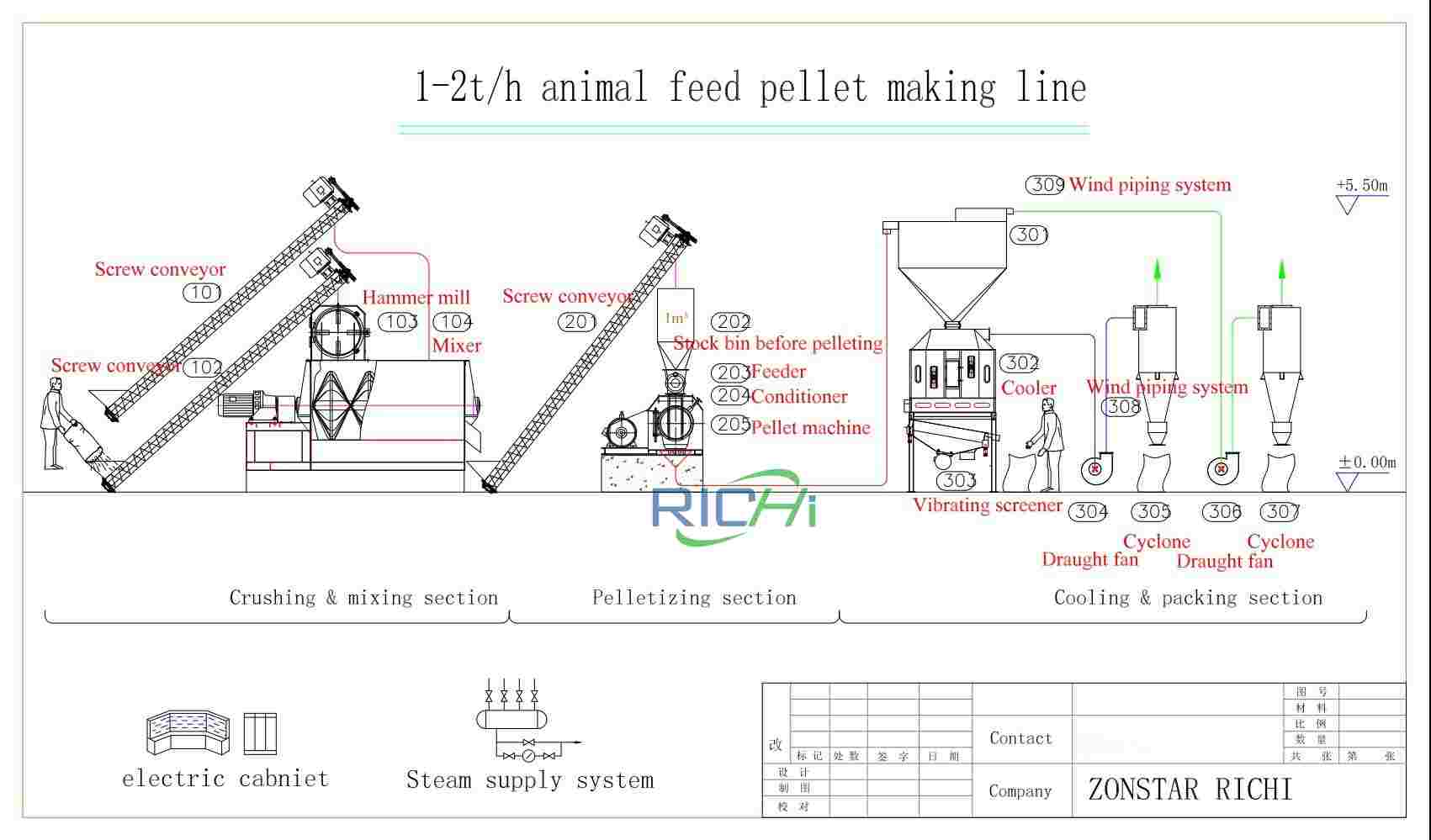
Crushing System
The first step in the production line is to crush the raw materials. Common raw materials include corn, soybean meal, and wheat. These raw materials need to be crushed to a suitable particle size for subsequent processing. The crushed materials will then move on to the next step.
Hybrid System
The crushed materials are evenly mixed through a feed mixer. Since the production of feed pellets usually requires multiple raw materials, the mixing process is crucial to ensure the nutritional balance of the feed and meet the growth needs of animals.
Granulation System
The mixed materials enter the granulation system. The materials are fed into the tempering device of the animal feed granulator through a feeder. The raw materials are gelatinized under high temperature and steam, and then pressed into uniform feed pellets under the pressure of the ring mold and the pressing roller.
Cooling System
Freshly made feed pellets are high in temperature and humidity, have a soft texture, and are prone to rupture. Therefore, it is necessary to cool the feed pellets to room temperature through a cooling system. This not only prevents the surface of the pellets from cracking but also extends the storage time of the feed.
Working Process of 35-40T/H animal feed processing plant
Large – capacity feed pellet production lines are suitable for large – scale breeding farms or feed processing plants, generally with a production capacity of 35-40 tons per hour. The main working processes of the large – capacity feed pellet production line are as follows:
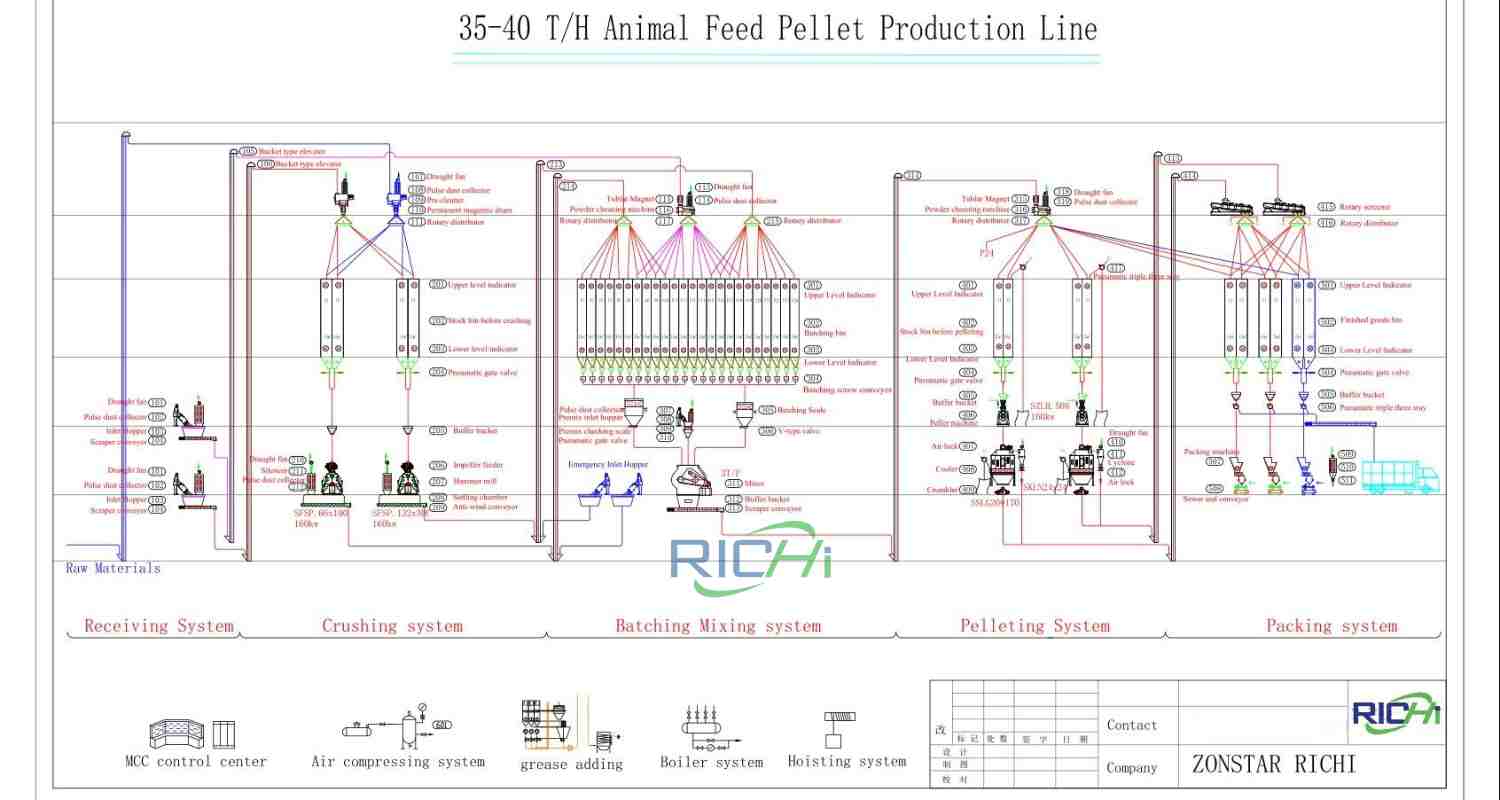
Cleaning and Crushing Systems
The raw materials are first fed into the feed hopper and conveyed vertically upward to the cleaning system through a bucket elevator. After preliminary cleaning by the drum – type pre – screening machine, iron impurities are removed by a permanent magnet cylinder, and then the materials are distributed to different silos. Subsequently, the raw materials enter a hammer crusher for crushing, and the crushed materials are sent to the silo through a bucket elevator for mixing.
Ingredient Mixing System
The ingredient scale is controlled by a computer to achieve accurate ingredient weighing, with an overall ingredient error of less than 3%. The mixing process is divided into three stages: First, the bulk materials enter the mixer and start to be mixed; then, the premix is placed in the small – material feed hopper for the second – stage mixing; finally, the grease is fed into the mixer through the grease – adding system, and the third – stage mixing begins. The mixed materials are fed into the pre – granulation chamber through a bucket elevator.
Granulation and Cooling System
The materials are fed into the tempering device through a variable – frequency speed – regulating feeder, where they come into contact with steam and are tempered. The tempered materials enter the ring die of the granulator. Under the strong extrusion of the ring die and the pressing roller, pellets are formed and then cut into the desired length by a cutter. A feed cooler is installed under the feed pellet mill for sale to cool the feed pellets to room temperature, preventing the surface of the pellets from cracking due to rapid cooling.
Automatic Packaging System
This system has a fully automatic bagging function. Equipped with equipment such as RICHI packaging machines with independent electrical control cabinets, the packaging weight can be set in the program to achieve automatic packaging operations, making the storage and transportation of feed pellets more convenient and efficient.
RICHI MACHINERY
Global case studies of animal feed processing plant
The following are some of the successful feed pellet project deliveries by RICHI Machinery. All these projects have adopted advanced feed pellet equipment designed by RICHI to meet the specific needs of customers.
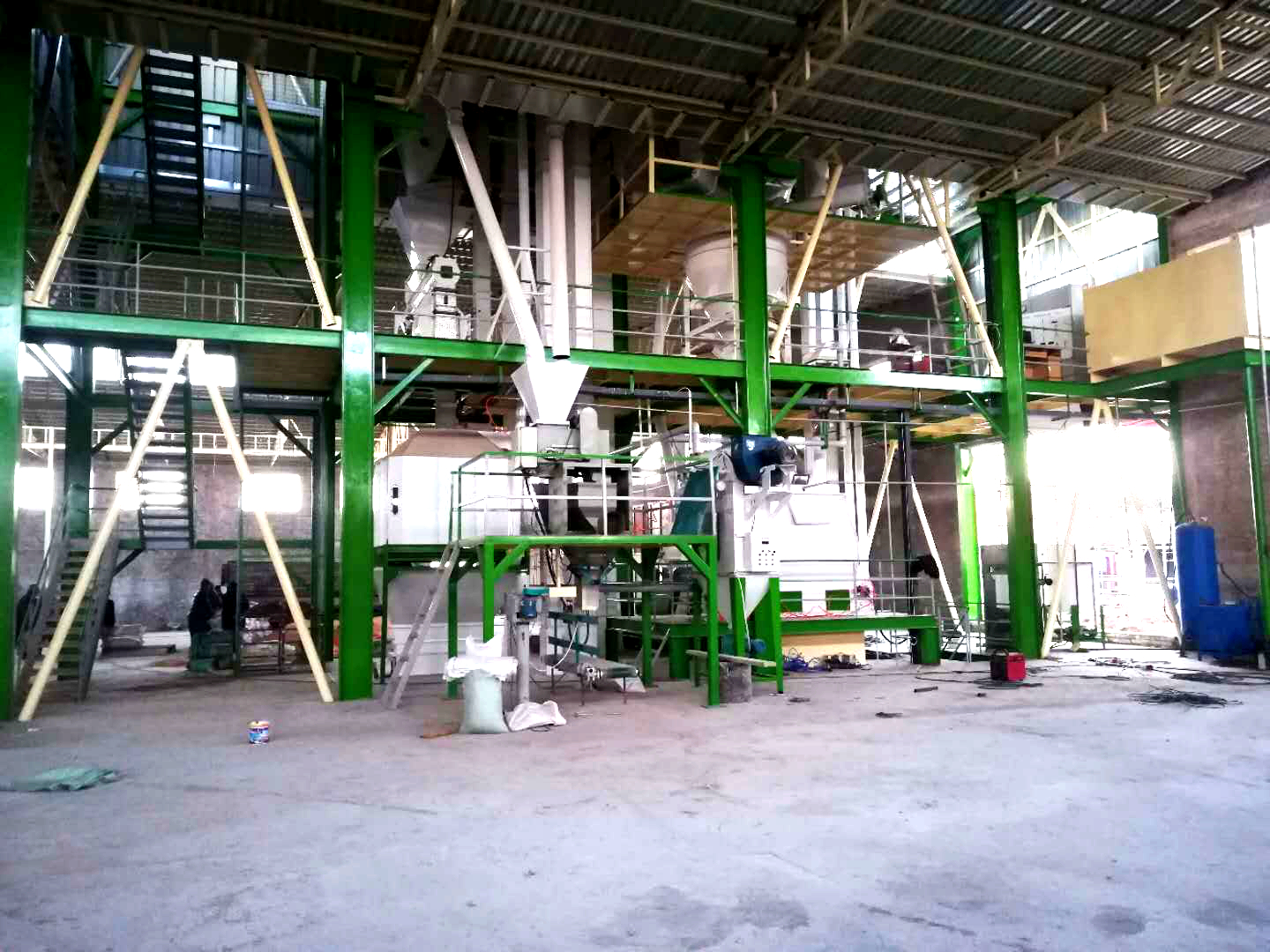
Indonesia 16 T/H Livestock animal Feed Pellet Machine
- Country: Indonesia
- Date: June 2018
- total Power: 805KW
- Project Workshop Area: 20000m²
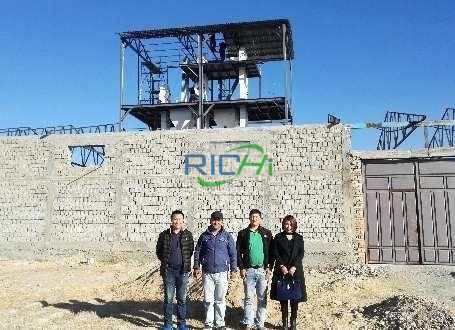
chicken feed production line in Uzbekistan
- Country: Uzbekistan
- Date: July 1, 2019
- Total Power: 520KW
- Project Workshop Area: 18000m²
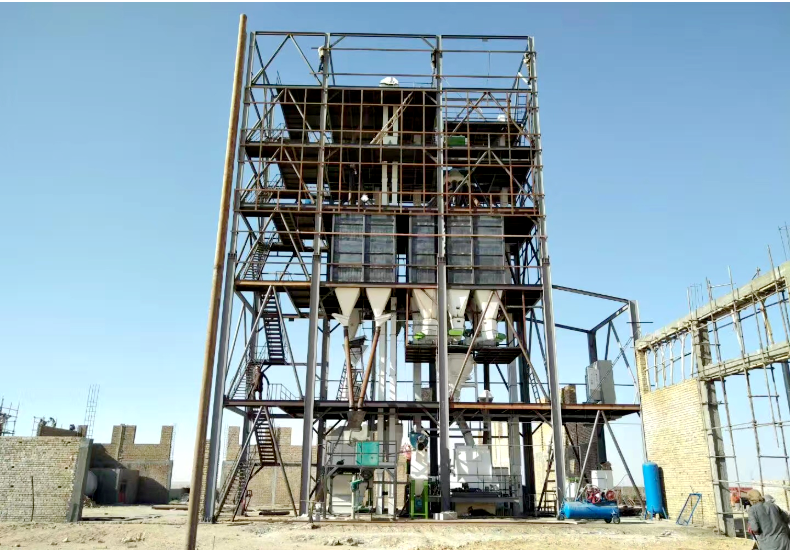
feed pellet machine south africa
- Country: South Africa
- Date: March 17, 2017
- Total Power: 335KW
- Project Workshop Area: 12000m²
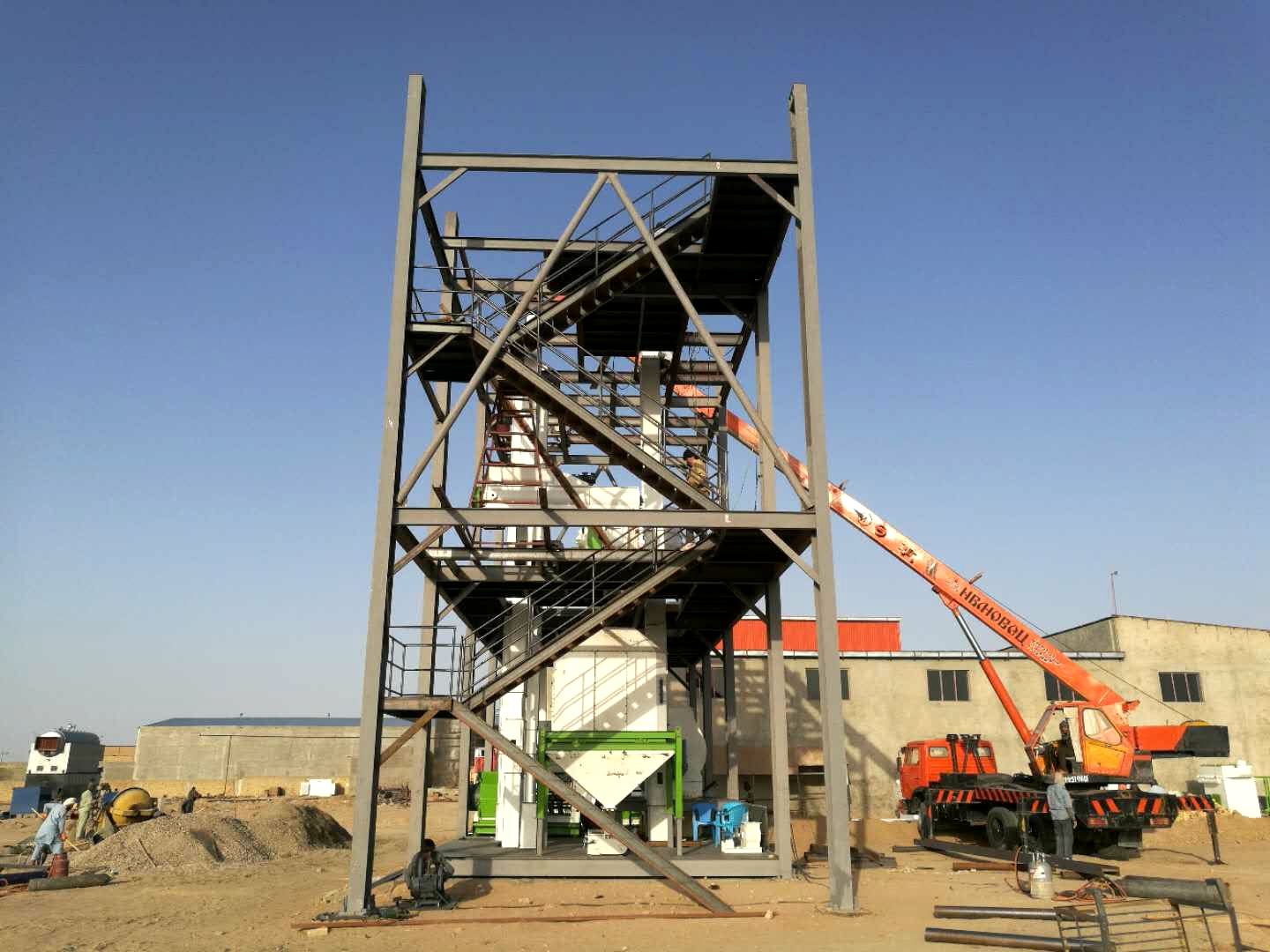
Afghanistan 10 – 15T/H Poultry animal Feed Manufacturing Plant
- Country: Afghanistan
- Date: November 18, 2017
- Total Power: 415KW
- Project Workshop Area: 19000m²
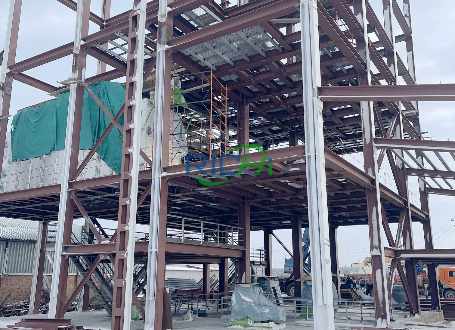
Ecuador 5T/H Fish Feed Pellet Line
- Country: Ecuador
- Date: November 21, 2017
- Total Power: 298KW
- Project Workshop Area: 7000m²
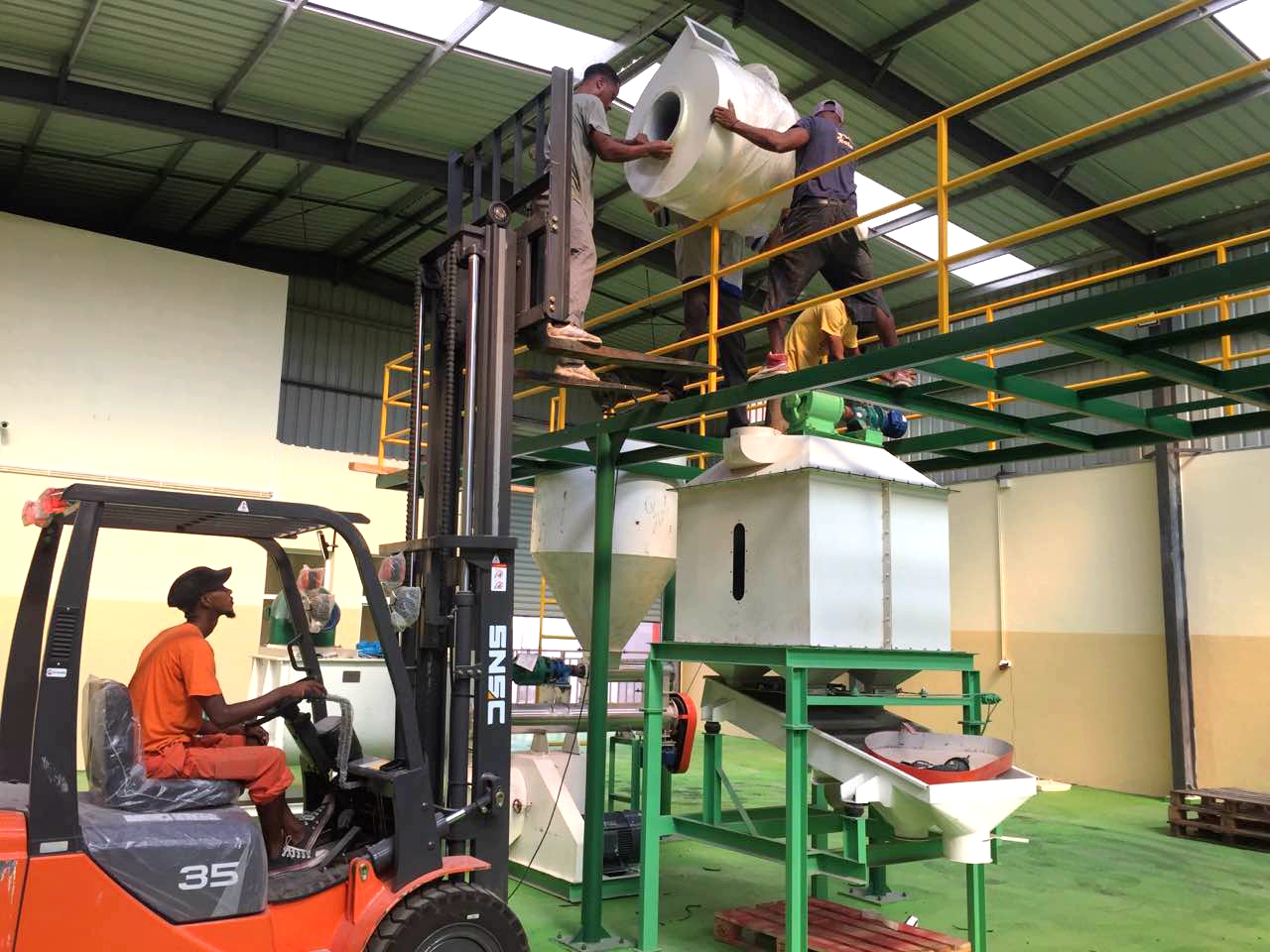
Nigeria 25T/H Chicken and Pig animal feed processing plant
- Country: Nigeria
- Date: October 2018
- Total Power: 795KW
- Project Workshop Area: 30000m²
Project Characteristics And Customer Feedback
— Richi Machinery —
(1) Customers are satisfied with the quality and service provided by RICHI Machinery, believing that its product performance is stable and the after – sales service is thoughtful.
(2)The professional technical team and installation engineers provide on – site guidance and training to customers, ensuring the smooth operation of the production line.
(3) RICHI Machinery provides tailored production line designs based on different raw materials, capacity needs, and local conditions, helping customers achieve maximum efficiency and cost-effectiveness.
(4) Customers have praised the equipment for its high output and low energy usage, which significantly reduces production costs while ensuring consistent pellet quality.

Frequently Asked Questions
Is the installation and debugging of the device complicated?
We have a professional technical team that provides customers with comprehensive installation and debugging services. Before the equipment is shipped, technicians will conduct comprehensive pre – installation and commissioning to ensure that the equipment is not damaged during transportation and can be quickly installed and put in place after arriving at the customer’s site.
After arriving at the site, technicians will install and fine – tune the equipment according to the customer’s site conditions and production needs. At the same time, they will provide detailed training to the customer’s operators to ensure that they are proficient in the operation and maintenance skills of the equipment. We will follow up the entire installation and debugging process to ensure the smooth production launch of the equipment.
Can the production capacity of the equipment be adjusted according to demand?
Certainly. Our feed production line fully considers the scalability of production capacity during the design phase. Customers can easily increase the capacity by adding equipment modules and upgrading key components according to actual production needs.
For example, they can increase the number of batching scales, expand the capacity of the mixer, and improve the production efficiency of the granulator to meet the growing production requirements of the company. At the same time, our technical team will provide customers with professional capacity – upgrade solutions and technical support to ensure the smooth progress of the upgrade process.
Do you provide installation and training services?
Yes, RICHI Machinery offer a comprehensive installation and training service to ensure that your equipment performs at its best. Our services include:
– Installation Training: We send experienced engineers to your site to guide the installation, commissioning, and trial operation of the production line. In addition, we provide your operators with comprehensive training to ensure stable and safe operation.
– Technical Support: Our dedicated service team can assist in solving any technical problems and ensure that your equipment runs efficiently.
– Regular Return Visits: We regularly track the equipment performance and solve any issues to ensure long – term customer satisfaction.
These services are part of our commitment to providing professional and convenient turnkey engineering solutions, from solution design and equipment production to installation, training, and ongoing technical support.
Does your equipment have ready – made spare parts?
Yes, our animal feed processing plant equipment has readily available spare parts. We maintain a comprehensive inventory of high – quality replacement parts to minimize customer downtime and ensure seamless operation. Whether it’s blades, hammers, screens, or other wearable components, our global supply network ensures fast delivery and easy access. In addition, our professional customer support team is available to help you select the right parts and provide maintenance guidance. You can find us on YouTube.